Share
Pin
Tweet
Send
Share
Send
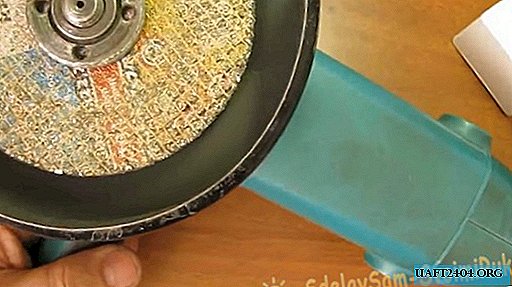
People who often use power tools sometimes encounter the following problem: the engine, whether it's a grinder, circular saw, plane or other equipment, starts very abruptly. Such a sharp start is fraught with many troubles: firstly, there is a high starting current, which does not affect the wiring in the best way, secondly, a sharp start of the engine quickly wears out the mechanical parts of the tool, thirdly, the usability decreases, when starting the grinder have to hold tight, she strives to break out of her hands. In expensive models, a soft start system is already built in, which easily copes with all these troubles. But what if this system is not? There is a way out - to assemble the softstarter yourself. In addition, it will be possible to use it with incandescent bulbs, because most often they burn out at the moment of switching on. Soft start will significantly reduce the ability of the bulb to quickly burn out.
Scheme
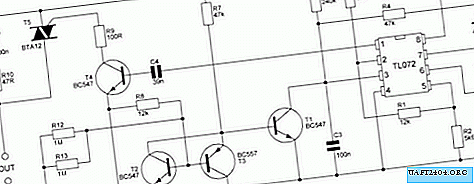
On the Internet, there is often a soft start circuit built on a rather rare domestic K1182PM1R microcircuit, which is now not always easy to get. That is why I propose an equally effective circuit for assembly, the key link of which is the affordable TL072 microcircuit, and LM358 can also be used instead. The time during which the engine is gaining full speed is set by capacitor C1. The larger its capacity, the more time it will take to disperse, the most optimal option is 2.2 microfarads. Capacitors C1 and C2 must be rated for at least 50 volts. Capacitor C5 - at least 400 volts. Resistor R11 will dissipate a decent amount of heat, so its power should be at least 1 Watt. Any low-power transistors can be used in the circuit, T1, T2, T4 have an n-p-n structure, you can use BC457 or domestic KT3102, T4 has a p-n-p structure, BC557 or KT3107 are suitable in its place. T5 - any suitable seven-cell power and voltage, for example, BTA12 or TC-122.
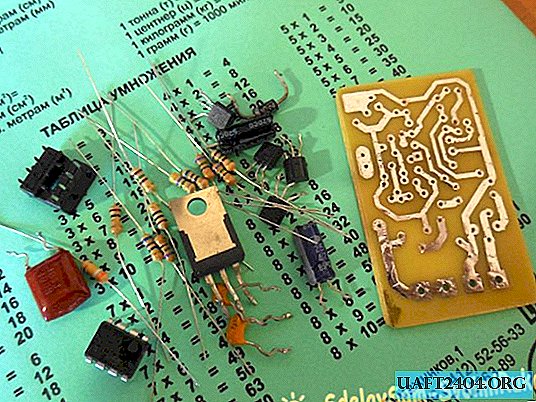
Making a soft start
The circuit is assembled on a printed circuit board measuring 45 x 35 mm; the circuit board is wired as compact as possible so that it can be built into the tool body, which requires a smooth start. It is better to solder the power wires directly to the board, but if the load power is small, then you can install the terminal blocks, as I did. The board is made by the LUT method, photos of the process are presented below.
Download board:
plavnyy-pusk-bolgarki.zip 20.96 Kb (downloads: 1118)
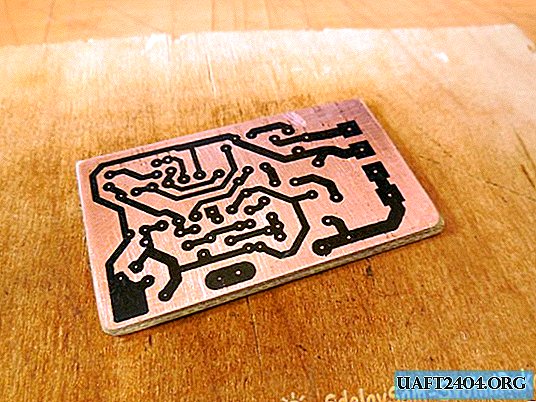
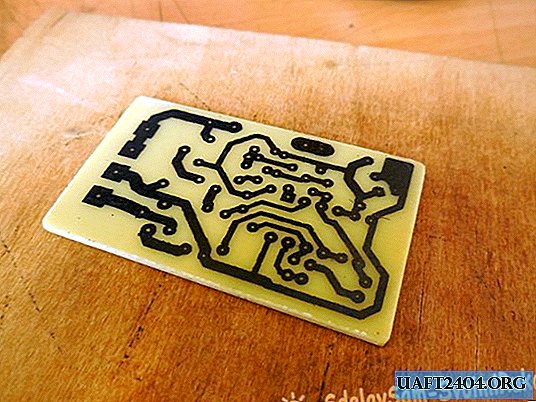
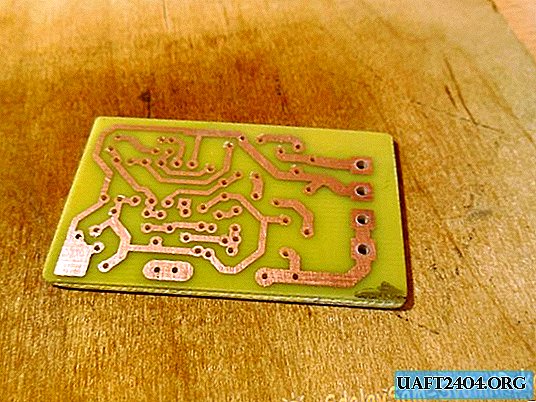
It is advisable to tear the tracks before soldering the parts, so their conductivity will improve. The chip can be installed in the socket, then it can be easily removed from the board. First, resistors, diodes, small capacitors are sealed, and only subsequently the largest components. After the assembly of the board is completed, it must be checked for proper installation, ring the tracks, wash the remaining flux.
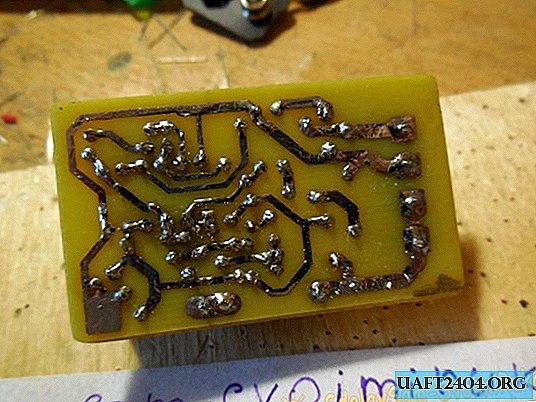
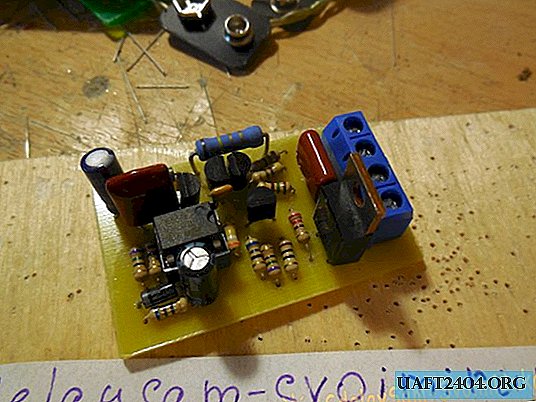
First launch and testing
After the board is completely ready, you can check it for performance. First of all, you need to find a low-power light bulb for 5-10 watts and through it connect 220 volts to the mains board. Those. the board and bulb are connected in series to the network, and the OUT output remains unconnected. If nothing on the board burns out and the light does not come on, you can connect the circuit directly to the network. The same low-power bulb can be connected to the OUT output for verification. When connected, it should smoothly gain brightness to the maximum. If the circuit works properly, you can connect more powerful electrical appliances. With prolonged operation, the seven-cell will probably heat up slightly - there is nothing to worry about. If there is free space, it will not hurt to install it on a radiator.
Hazardous mains voltage is present on the board during operation; therefore, safety precautions must be observed. In no case should you touch the details of the board when it is connected to the network. Before switching on, make sure that the board is securely fixed and that metal objects that could lead to a short circuit will not get on it. For reliability, it is recommended to fill the board with varnish or epoxy resin, then even moisture will not be afraid of it. Successful assembly!
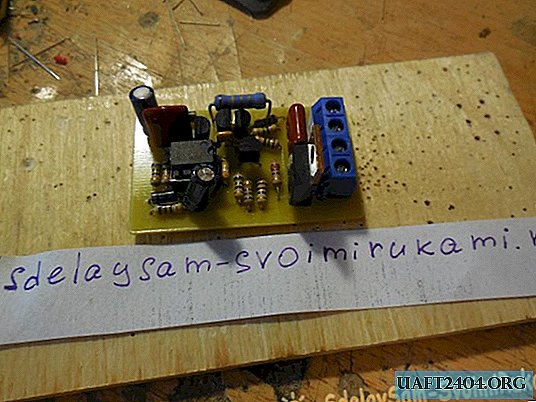
Watch the video of work
Share
Pin
Tweet
Send
Share
Send